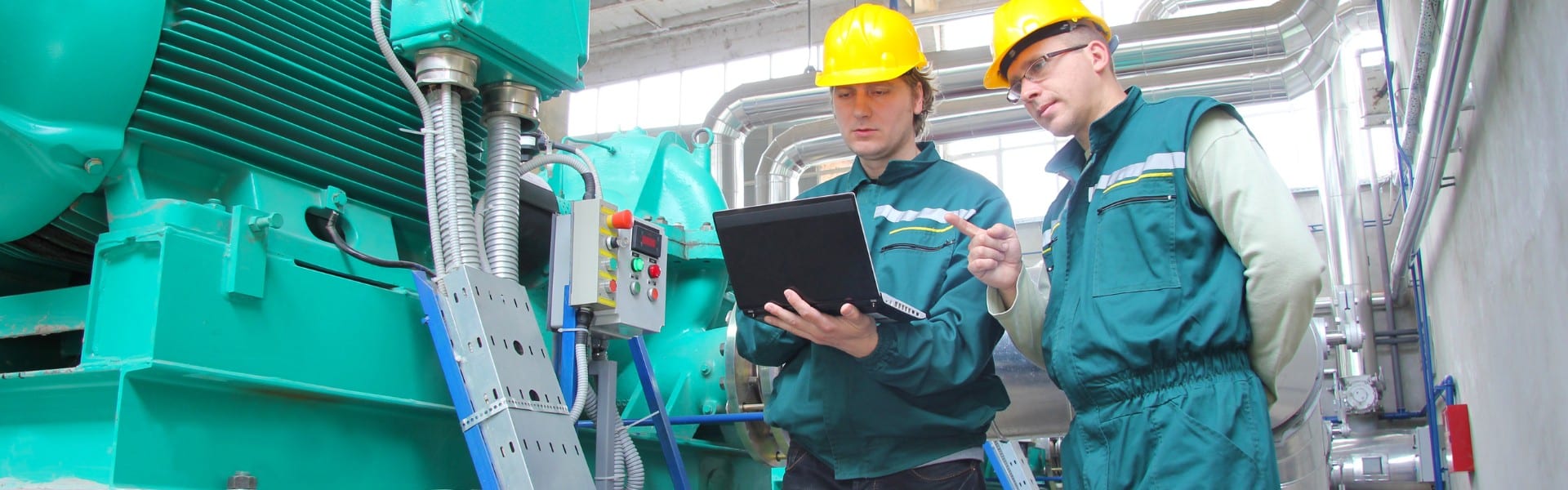
OT-security
The forgotten risk:
Why OT security is crucial for your business
Operational technology (OT) keeps your manufacturing business running. Machines, sensors and systems ensure that everything keeps running smoothly. But what about the security of such technology? While IT systems are well protected, OT systems remain vulnerable. Hackers are well aware of this and are increasingly targeting these weak spots.
The result? Production downtime, financial losses and dangerous situations on the shop floor. Tyneso explains why OT security is a forgotten priority, which risks this brings and what companies can do to protect themselves better.
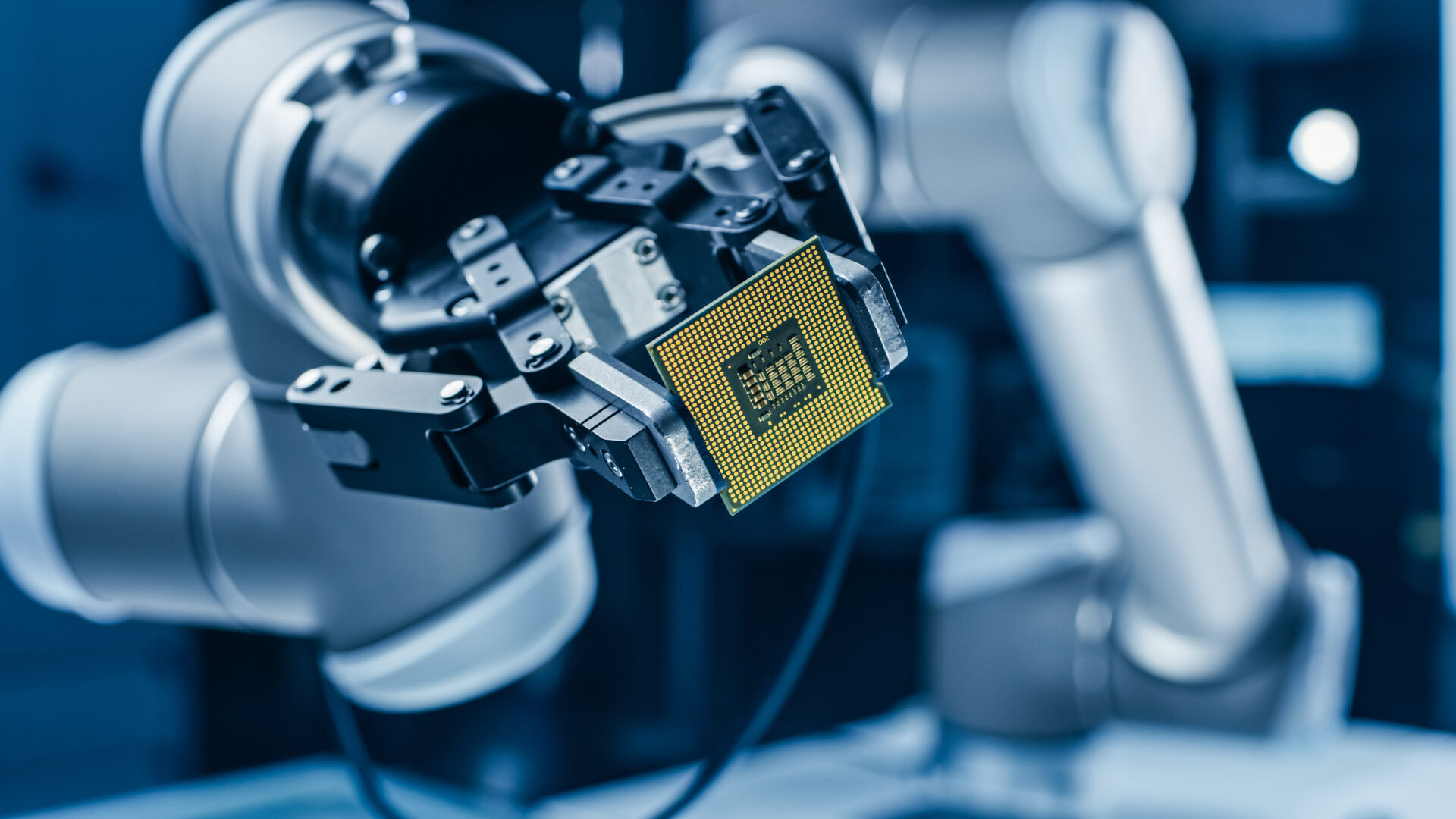
What is OT and why does it differ from IT?
Operational technology (OT) controls physical processes. Examples are assembly lines, robotic arms or sensors that monitor the temperature and pressure in your factory. OT is the heart of your production process: without OT, everything stops and no finished product rolls off the line.
Although IT and OT are often mentioned together, they are fundamentally different:
- IT is about data: storing, processing and sharing information.
- OT ensures physical processes keep going, such as controlling machines and production lines.
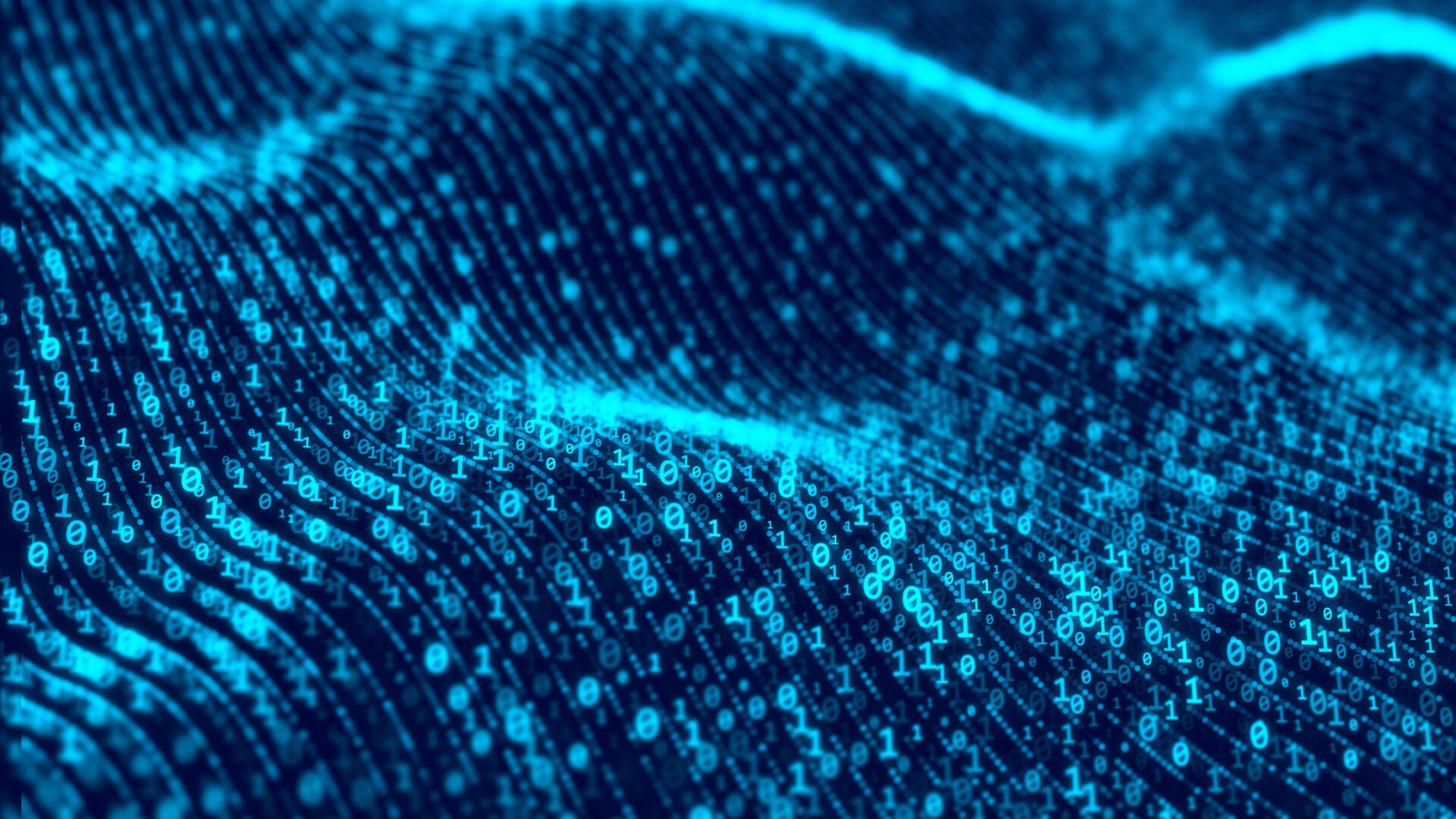
The big problem? Many OT systems are outdated and run on software that was never designed with cybersecurity in mind. Hackers can gain access to your factory via vulnerabilities in operational technology. Imagine an attack that causes machines to suddenly stop or sensors to report incorrect values. This leads not only to downtime, but also to hazardous situations and high costs.
What is OT security?
OT security refers to the complete set of hardware and software used to monitor, detect and control changes to devices, processes and events. It’s used to protect industrial systems and networks from cyberattacks. For example, systems that safeguard critical infrastructures, such as electricity plants, transportation networks and smart city devices.
OT security specifically focuses on protecting operational technology from risks like:
- Unauthorised access to systems
- Manipulation of production processes
- Failure of industrial installations
You’ve probably heard the terms SCADA and ICS before. But what do they actually mean?
- SCADA (Supervisory Control and Data Acquisition):
SCADA is a system that monitors and controls industrial processes remotely. For example, systems that manage water pressure in a water supply or control the power distribution in an electricity grid. - ICS (Industrial Control Systems):
ICS is an umbrella term for systems that control and safeguard industrial processes. This can range from alarms in building management systems to managing production equipment in a factory.
Why is OT security essential?
SCADA and ICS systems are the beating heart of many industrial operations. They’re essential for smooth operations, but are also vulnerable to cyberattacks. If these systems are manipulated, it can cause downtime, quality issues or even safety incidents. Securing this infrastructure is no longer an option, it’s an absolute necessity.
Why is OT security
so often overlooked?
OT does its job: it works and keeps your manufacturing business running. Many companies adopt the mentality: “If it’s not broken, don’t fix it.”
Furthermore, production continuity is often the top priority, causing security updates or investments in OT security to be postponed in order to avoid downtime. However, this approach carries significant risks.
OT systems are often outdated, managed separately from IT and are hard to update without disrupting production. Hackers are well aware of this and take advantage of it. Without proper security, your manufacturing business becomes an easy target.
What are the risks of
unsecured OT systems?
Unsecured OT systems pose significant risks, from production downtime to reputational damage. The impact of cyberattacks on operational technology is growing every year. According to the Fortinet 2024 report, more than half of the companies experienced an OT breach in the past year. These are the key consequences:
- Operational downtime: Almost 55% of the organisations reported a complete interruption of their manufacturing processes. Hackers disable systems, leading to major delays, lost revenue and pressure on customer relationships.
- Loss of data: Most affected companies lost sensitive business information or intellectual property, such as production data or customer information. For 43% of the organisations, this involved critical data with long-term repercussions.
- Repeated attacks: While most companies are affected sporadically, a small but significant group reported experiencing more than six breaches a year.
The consequences are not only operational, they also affect a company’s reputation. More than half of the businesses reported a clear decline in customer trust and brand value after an OT breach—a problem that has only worsened over the past year. Just remember the cyberattack on Duvel Moortgat in 2024 and the hacking of meat processor Dekeyzer-Ossaer in 2019.
Meanwhile, cybercriminals continue refining their methods. Phishing remains by far the most common form of attack (76%), followed by ransomware and business email compromise. The rapidly growing threat emphasises the need for a strong OT security strategy to protect business processes and minimise risks.
What can you do to reduce your OT risks?
The first step? Recognise that OT is just as vulnerable as IT. Many companies are simply unaware of the risks. That’s why it’s important to take action now and address the security of your OT systems.
- Keep OT and IT systems separate. Ensure that they’re not directly connected, so that a breach in IT does not automatically impact OT, and vice versa.
- Check that your OT systems are up to date. Many attacks occur through outdated software or poorly secured connections. Regular updates and monitoring are essential. But what if a system can’t be patched immediately or is no longer supported? In this case, Tyneso, with the help of Fortinet technology, can provide virtual patching. This offers an extra layer of protection, by shielding weak spots, without requiring changes to the underlying software.
- Train your employees. Cyberattacks often begin with human errors, such as an unprotected USB stick or a suspicious link. Awareness can prevent many risks.
- A proactive approach, such as a secured production network, can protect your manufacturing business from modern threats.
Most importantly: choose a reliable partner who, as well as providing insight into your vulnerabilities, also offers the right strategy and technology to properly secure your production environment.
Conclusion
Operational technology is the backbone of your manufacturing business. However, without the right security, that foundation is very vulnerable. OT security is often overlooked, yet the consequences of an attack are simply too severe to ignore.
Grow without concerns? Choose a secure manufacturing environment!
Would you like to learn more about how to make your manufacturing environment safer?
Related content
We are happy to share our expertise with you! Read more valuable tips for your business!